As a production and procurement manager with over 10 years of experience in the footwear industry, I'm constantly looking for ways to increase efficiency without compromising quality. Our factory processes thousands of shoe uppers daily, and traditional line marking methods were becoming a serious bottleneck — slow, labor-intensive, and inflexible when switching between styles.
NAME | SPECIFICATIONS |
Dimension | L3700 * W2020 * H2339 (mm ) |
Working Area | 1220 * 850 (mm ) |
Marking Speed | 1500mm/s |
Precision | Accuracy deviation ≤ ±0.5mm |
Number of Print Heads / Nozzles | 2 high-precision inkjet nozzles |
Driving Mechanism | Dual servo motors + dual linear guide rail system |
Positioning System | High-resolution industrial camera + visual recognition system |
Supported File Formats | Supports PLT, DXF, AI, BMP, JPG and other common formats |
Operating System | Windows system + self-developed marking software |
Rated voltage | 3 -5 Kw |
Power supply | AC 220V ±10% 50HZ |
Air Pressure | 0.6-0.8 Mpa |
Working mode | Dual-head inkjet (MarkJet) |
Applicable Materials | Compatible with various upper materials: synthetic leather, genuine leather, mesh, etc. |
Capaticy | Average 1500-2500 Pieces / H |
Consumable parts | Nozzle, Plunger |
Consumables | Heat Erasable Ink, FluoMark Ink, UVPrint Ink, Thermochromic Ink, DeepBlack Ink, SoleMark Ink |
Applicable ink types | Heat sensitive ink, High-temperature disappearing ink, fluorescent ink, others |
- Footwear manufacturing (sports shoes, safety shoes, kids’ shoes, fashion sneakers, etc.)
- Leather goods production (bags, gloves, leather accessories, etc.)
- Apparel and garment accessory processing (pre-marking for sewing alignment)
- Smart manufacturing & flexible production lines
- All types of upper fabrics (canvas, non-woven, Oxford, etc.)
- Synthetic leather: PU, PVC
- Genuine leather, suede
- Mesh, breathable fabrics, functional composite textiles
- Multi-layer laminated materials (auto-detected without preprocessing)
- Stitching guideline marking for shoe upper components
- Positioning lines for shoe templates
- Pre-cut alignment graphics
- Contour printing of large-scale patterns
- Synchronous marking for multi-part processing

- Up to 800–1200 pairs per hour throughput. One machine can replace 2–3 skilled workers and serve two production lines efficiently.
- Precision down to ±0.5mm using industrial vision alignment — ensuring consistent marking quality across all components.
- No template needed for design switching. Start a new production batch in under 60 seconds. Perfect for mixed-style production lines.
- Low ink consumption & minimal maintenance, with printhead lifespan over one year and remote diagnostics support.
- Trusted by major international brands like Nike, PUMA, Skechers, and Timberland — enhancing your factory’s credibility in client audits.
- Qualifies for smart manufacturing subsidy programs in some regions, with payback achievable within 6–12 months.
- This is more than a machine — it's a future-proof investment in your factory’s global competitiveness.

Chart 1: Manual Labor vs Equipment ROI – 12-Month Comparison
Orange Line: Cumulative labor cost using 3 workers manually (approx. ¥30,000/month)
Red Line: Equipment cost (¥80,000 in month 1, then ¥2,000/month)
Dashed Line: Estimated payback point — machine becomes more cost-effective starting month 4

Chart 2: Manual Labor vs 1610J– Daily Productivity Comparison
Orange bars: Manual marking output (approx. 150 pairs per worker per day)
Coral bars: 1610J output (approx. 1000+ pairs per day regardless of operator count)
Conclusion:
The machine enables a single operator to outperform a 3-person manual team by more than 2x, offering unmatched scalability and consistency.
Before (Left Image) | After (Right Image) |
![]() | ![]() |
|
|
💬 Customer Testimonials
🌎 Diego S. – Brazil
“We’ve increased our daily output by 2.5x thanks to the 1610J. The line accuracy is incredible, and the software is surprisingly easy to use. It helped us meet a tight deadline for a major sports shoe brand.”
— Production Manager, São Paulo
🌍 Mr. Ahmed – Egypt
“We replaced three manual stations with just one machine. The ROI was faster than expected. PUBA’s team gave excellent online support, and we’ve had zero downtime in 6 months.”
— Factory Owner, Cairo
🌏 Nguyễn T. – Vietnam
“Our clients loved the quality improvement. No more complaints about stitching alignment. The vision system is very stable, and it works well with mesh and PU uppers.”
— Shoe Manufacturing Engineer, Ho Chi Minh City
🌍 Carlos M. – Mexico
“1610J helped us win two new brand orders. The marking is sharp and professional, and switching designs only takes seconds. Definitely the best investment this year.”
— Operations Director, León
✅ Customer Success Story
🏭 Client Profile
Factory Name: Confidential (Indonesia)
Industry: Footwear OEM for International Brands
Scale: 800+ employees, monthly output > 300,000 pairs
Target Brands: OEM for global names including sportswear and safety footwear
✨ Project Background
The Indonesian client was seeking a reliable solution to improve the accuracy and efficiency of upper line marking. Their traditional marking process, which relied on screen printing and manual templates, led to frequent alignment issues and time-consuming rework — especially for complex designs demanded by international brands.
After a comprehensive evaluation, the factory chose PUBA's 1610J High-Speed Dual-Track Intelligent Marking Machine for its superior performance, automation capabilities, and proven success with global OEM factories.
⚙️ Deployment & Implementation
Machines Deployed: 6 units of 1610J
Production Lines Covered: 3 parallel lines
Materials Used: mesh fabric, synthetic leather, laminated uppers
Operators Required: Only 1 per machine
📸 Factory Setup Snapshot:

📈 Results After Integration
Metric | Before | After 1610J Deployment |
Daily output per station | ~300 pairs | 1000+ pairs |
Labor per station | 2 skilled workers | 1 semi-skilled operator |
Marking error rate | 4.3% | <0.3% |
Design switching time | 20–30 minutes | < 1 minute (instant file switch) |
Rework or reprint cost | High | Significantly reduced |
Brand audit pass rate | Improved to 100% |
💬 Customer Feedback
“The 1610J machines have become a critical part of our automation strategy. They help us meet international brand requirements more easily, with consistent precision and fast switching between designs. We plan to expand deployment to more lines next year.”
— Engineering Director, Indonesia Plant
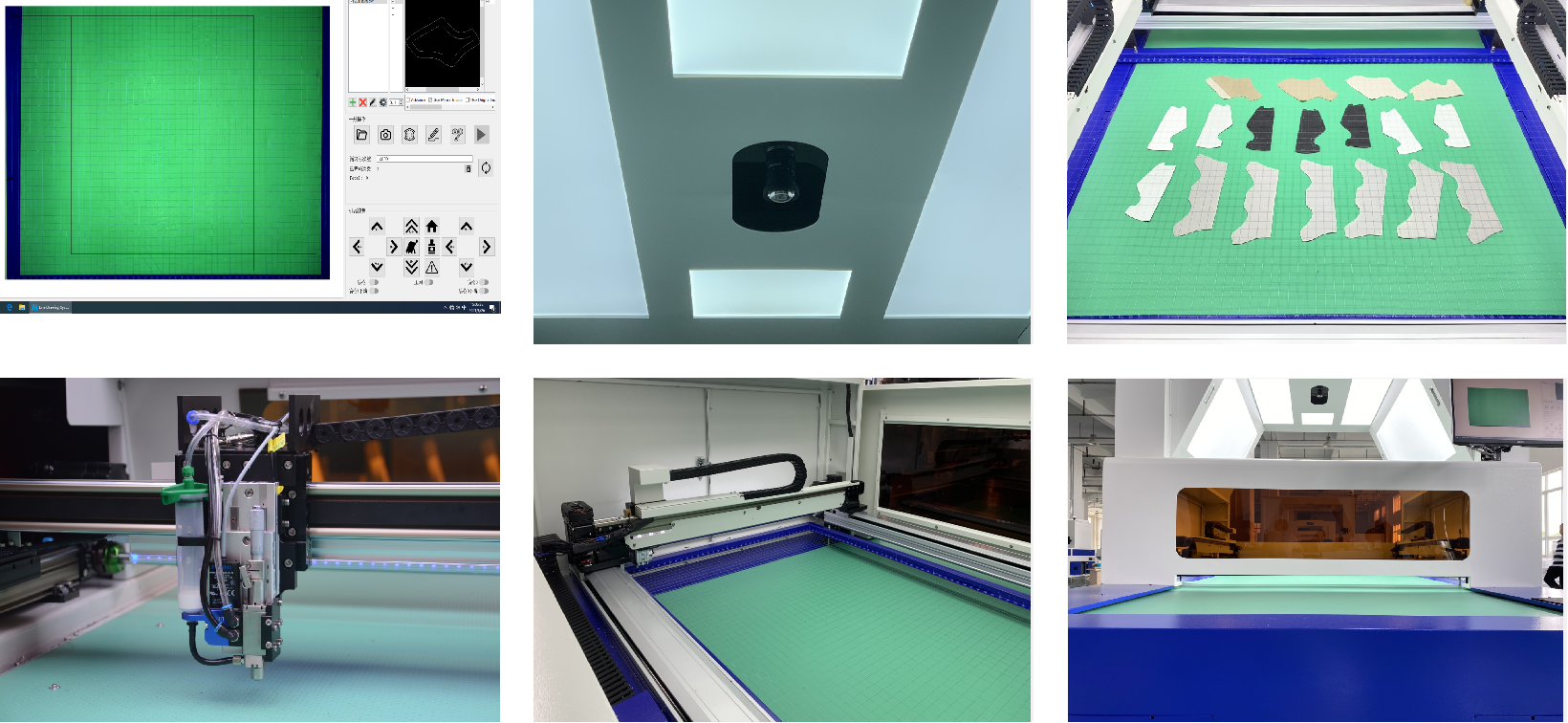